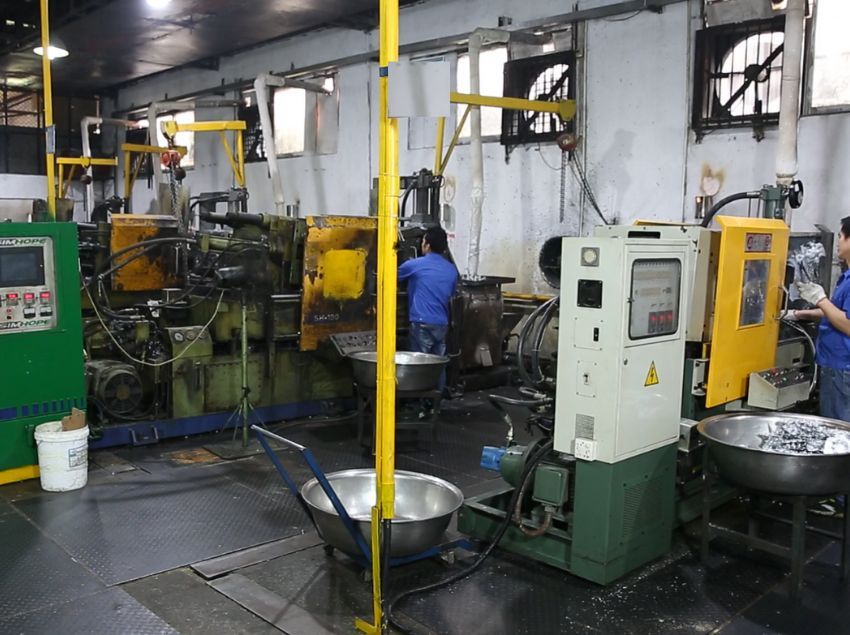
Zinc Alloy Custom Medals and Emblems
Zinc alloy's popularity stems from its versatility and affordability. Its ability to be molded into intricate designs makes it a top choice for creating visually appealing pin badges, emblems, and medallions. Whether it's a simple 2D design or a complex 3D cubic masterpiece, zinc alloy can bring your vision to life. Not only is it perfect for intricate cutouts and miniatures, but it also excels in designs with moving parts like hinges, sliders, or spinners. Compared to brass, zinc alloy offers a cost-effective alternative without compromising on quality.
- Video
In the video demonstration, the installation of zinc alloy molds emerges as a time-intensive procedure. To streamline this operation, a common practice involves combining molds of varied designs into a singular unit, the consolidated mold is then moved to the injection chamber using a lifting machine due to their substantial weight. Typically, this composite mold comprises molds with similar production quantities to enhance operational efficiency. The market demand for zinc alloy products has led to a reduction in the minimum order quantity (MOQ) for zinc alloy souvenirs, decreasing from 500 pieces to 100 pieces, aligning more closely with prevailing market trends.
Zinc alloy must be heated to the liquid stage, so the molten zinc alloy can be injected through channels into the die casting molds. Since all the shapes are casted, it is a perfect material for making custom medals, lapel pins, personalized keychains in complex shapes, 3Ds, miniatures, or designs with empty spaces in between. By combining multiple smaller molds into a larger one, we create injected items with various interconnected designs that are later separated manually. This process is known as die casting.
The mold for zinc alloy is composed of several designs combined into a large mold, with each mold having channels connecting through one another. The liquid zinc alloy is injected into the molds through these channels, creating a considerable amount of scraps. After the injected parts cool down, the scraps are removed, collected, and melted into zinc alloy ingots for use in the next production cycle.
Riveting attachments such as safety pins, nails, and cufflinks onto zinc alloy products is a practical choice due to the low melting point of zinc alloy. Soldering, which requires high heat, can cause the zinc alloy to melt or deform, compromising the integrity of the attachment. Riveting, on the other hand, provides a secure and durable connection without the risk of damaging the zinc alloy. This method ensures that the attachments remain firmly in place, making the final product reliable and long-lasting.
- Gallery