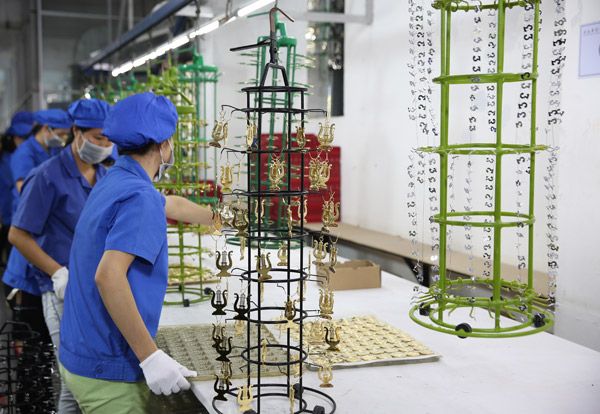
Electroplating for Lapel Pins, Challenge Coins, Medals, and More
The electroplating process not only protects the metal surface but also gets the desired color on the metal. The emblems attached to the racks are automatically transported from one location to another through the automated electroplating line. The time for immersing in the plating chemicals is precisely controlled by a computer. Once the electroplating procedure is completed, the emblems are conveyed along a track and removed from the racks. Each emblem is then individually protected and waiting to proceed with the next procedure.
- VideoGallery
This video introduces the electroplating process in our metal factory. Our automated electroplating line has obtained a license from the Chinese government and is equipped with a wastewater treatment plant to eliminate pollutants before the discharge is released into the river. The automatic plating process, featuring rotation along the axis, replaces manual operation, resulting in an even finish. Furthermore, it reduces the chance of human error and premature judgment.
This is the racking process, during which we carefully arrange emblems piece by piece and hang them on the rack using pins, rings, safety pins, or any attachment that won't leave marks on the emblems. We consider different racking methods for different fixtures to ensure quality and precision. Maintaining the right balance is crucial—items should neither be hung too tight, which can cause marks after electroplating, nor too loose, which may result in dropping during transportation.
In an effort to enhance quality control, meet production schedules, and create a safer working environment, this in-house automatic electroplating line has been established. Every step, including the time of chemical submersion, dipping, and retrieval from the chemical fluid tanks, is computerized and automated. Each rack is hung on the conveyor and transported from location to location without colliding.
After the electroplating process, the racks are hung on the conveyor and sent to the production lines for the removal of emblems from the rack. Each emblem is carefully inspected and placed in trays before proceeding to the next step.
Barrel plating is an economical choice for customers looking to efficiently plate a high volume of metal emblems and attachments at lower costs. By utilizing rotating barrels to hold the items during the plating process, this method allows for a uniform coating on multiple pieces simultaneously. The lower equipment costs and reduced labor requirements make barrel plating an attractive option for businesses seeking to balance quality with affordability.
In this process, each emblem is coated with a layer of lacquer for protection. This step is particularly crucial for emblems with antique finishes, preventing them from oxidizing after exposure to the air.
This is a page from history when all the electroplating procedures were done manually. Each rack had to be moved from tank to tank by hand. We have improved ourselves and progressed with time. The old electroplating tanks have become obsolete and have been replaced by advanced electroplating line that is highly computerized and fully automated.